Single Use Instruments
Manufactured from medical grade surgical steel, the instruments are packed in a Class 7 Cleanroom and sterilised in twin chamber steam autoclaves, which are independently certified to meet rigorous quality standards.
In a hospital setting, it has been found that costs can be significantly lower using single use instruments rather than reusables – even though on site sterilisation facilities exist.
It is important when comparing costs to take into account the full cost of using reusables. Have you taken into account the following?
- Capital cost of premises and developing the facility, decontamination and sterilisation equipment
- All staff costs including recruitment, training, absence, inefficiency (utilisation), HR cost
- Management and administration costs
- Cost of ongoing maintenance and validation of decontamination and sterilisation
- Consumables used
- Capital cost of instruments and the replacement of any lost
- Repair costs
- Transport costs
- Traceability system costs
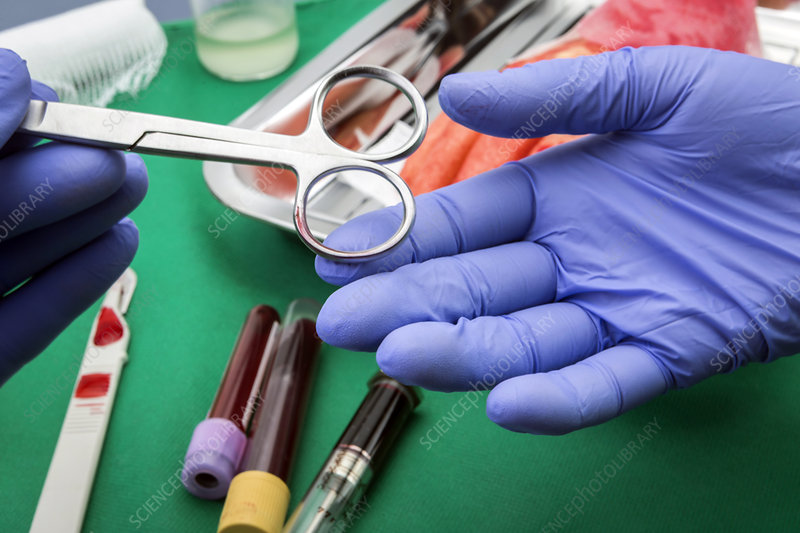
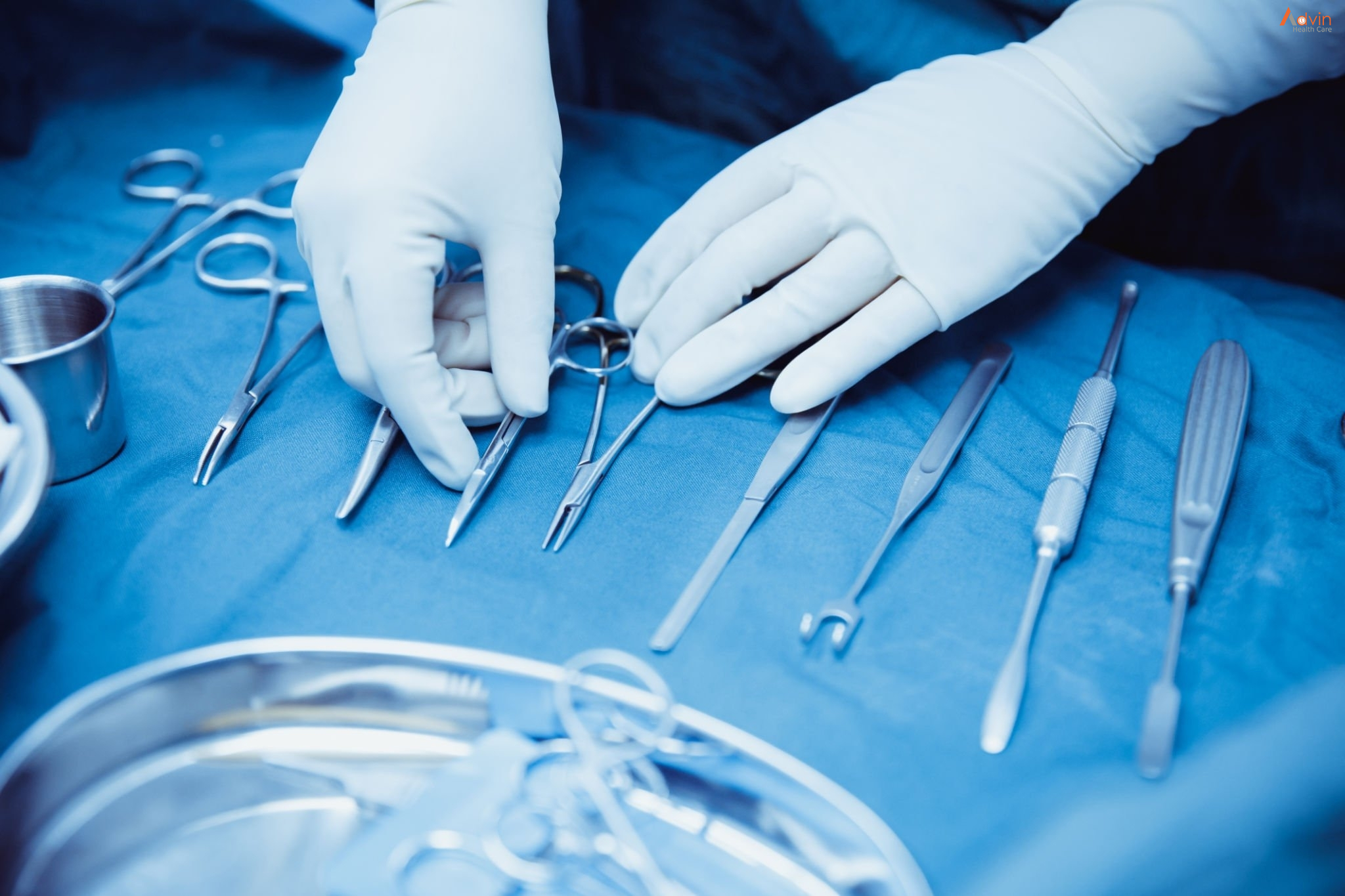
If you are considering using a third party steriliser, have you taken into account the following?
- Capital cost of instruments
- Lost instruments
- Repairs
- Transport cost to and from the steriliser
- Increase in instrument stock required to cover longer turnaround times
Instrapac single use instruments can contribute to reducing time lost in the following ways:
- Eliminate the need to check instruments for wear & tear prior to use
- No waiting for instrument collection
- No delays in supply due to sterilisation capacity issues
- No supply shortages due to lost instruments or waiting for repairs
- No supply shortage – Instrapac is in stock and delivered rapidly when ordered
- Instruments work correctly every time
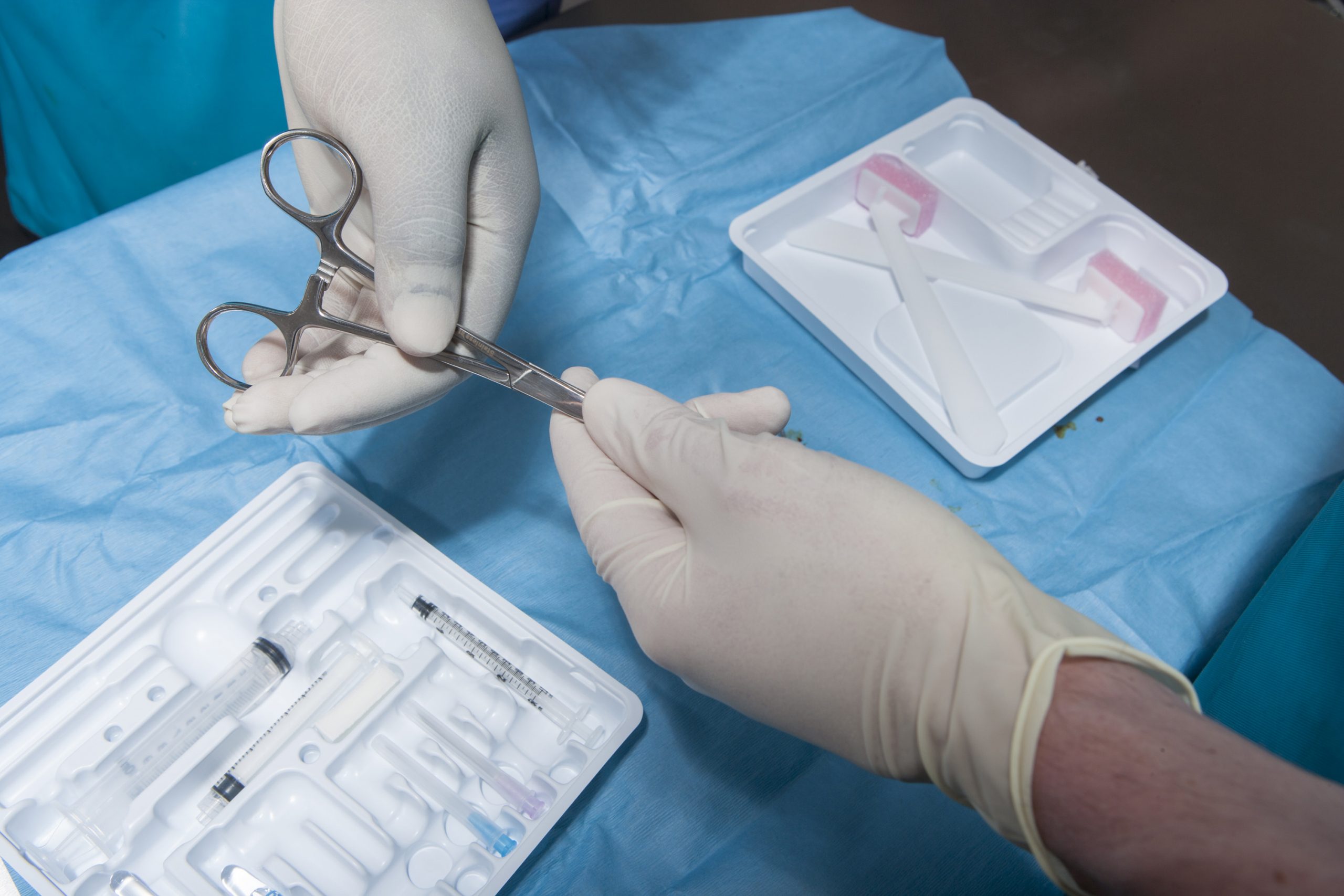
Emerald Healthcare Ltd with our partner Vernacare retain control over the production of Instrapac products by checking, packing and sterilising in the UK at the company’s large manufacturing facility. A large Class 7 cleanroom provides hygienic packing facilities, with sterilisation carried out in the onsite twin chamber steam autoclave or at an EO gas sterilisation facility in the UK.